СКАЧАТЬ РАБОТУ БЕСПЛАТНО -
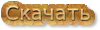
Глава 1. Роль управления качеством при организации производства в компании
1.1. Сущность и особенности японской школы управления качеством
Вся японская школа управления качеством основана на системе всеобщего управления качеством (TQM) [2].
Всеобщее управление качеством (Total Quality Management) – это философия организации, которая основана на стремлении к качеству и практике управления, приводящей к всеобщему качеству.
Всеобщее управление качеством – это новый подход к управлению любой организацией, нацеленный на качество, основанный на участии всех ее членов (персонала во всех подразделениях и на всех уровнях организационной структуры). Подход направленный на достижение долгосрочного успеха посредством удовлетворения требований потребителя и выгоды, как для сотрудников организации, так и для общества в целом [12].
Основными целями TQM являются:
- ориентация предпринимателя на удовлетворение текущих и потенциальных запросов потребителей;
- возведение качества в ранг цели предпринимательства;
- оптимальное использование всех ресурсов организации .
Основные элементы модели TQM представлены на рисунке 1.
Как видно из рисунка, наиболее важными элементами TQM являются:
- Вовлеченность высшего руководства: стратегия качества в компании (организации) должна предусматривать постоянное, непрерывное и личное участие высшего руководства (руководителя) компании в вопросах, связанных с качеством.
- Акцент на потребителя: фокусировать всю деятельность компании на нужды и пожелания как внешних, так и внутренних потребителей.
- Всеобщее участие в работе: обеспечивать возможности для реального участия каждого в процессе достижения главной цели – удовлетворять запросы потребителя.
Рисунок 1 - Элементы системы TQM
- Внимание процессам: фокусировать внимание на процессах, рассматривая их как оптимальную систему достижения главной цели – максимизации ценности продукта для потребителя и минимизации его стоимости, как для потребителя, так и производителя.
- Постоянное улучшение: постоянно и непрерывно улучшать качество продукта.
- Базирование решений на фактах: базировать все решения компании только на фактах, а не на интуиции или опыте ее работников .
Управление качеством – это динамично развивающаяся концепция. На сегодня существует несколько основных «школ» ТQМ (японская, американская, европейская). Возможно, поэтому в среде специалистов нет единого мнения о количестве принципов, на которых базируется ТQМ. Основными же признаны следующие восемь:
- Ориентация организации на потребителя.
- Роль руководства.
- Вовлечение сотрудников.
- Процессный подход.
- Системный подход к управлению.
- Постоянное совершенствование.
- Принятие решений, основанное на фактах.
- Взаимовыгодные отношения с поставщиками.
Организация, применяющая концепцию ТQМ, должна систематически собирать и анализировать информацию, поступающую из самых различных источников и позволяющую получать обоснованные выводы относительно текущих и потенциальных потребностей как отдельных потребителей, так и рыночных сегментов и рынка в целом [20].
Для того чтобы осуществить принцип ориентации на потребителя, необходимо предпринять следующие действия:
- изучение спроса с целью полного понимания потребностей и ожиданий потребителя в отношении товаров, цен, поставки и т.д.
- обеспечение сбалансированности в запросах потребителей и других участников сделки с товарами (собственников бизнеса, персонала организации, поставщиков организации, общества).
- измерение потребительской удовлетворенности с целью коррекции собственной деятельности.
- управление взаимоотношениями с потребителями.
Компания должна стараться узнать мнение своего потребителя и затем с помощью «обратной связи» произвести корректировку параметров качества продукта с целью его улучшения для пользователя.
В практике управления качеством наиболее широко используются два основных канала «обратной связи» [15]:
- обратная связь для корректировки и улучшения товара при сопоставлении его с аналогичными товарами других производителей.
- сбор данных и интерпретация ожиданий потребителей, проводимых по особым каналам, которые обычно курируют отделы сбыта и маркетинга
Если руководитель компании не проникся необходимостью ТQМ для успеха в конкурентной борьбе за потребителя, то, как показывает мировая практика, «борьба за качество» останется только лозунгом. Руководитель должен включать аспекты качества в цели компании и поддерживать ее деятельность финансированием качества, моральными стимулами и возможностями ресурсов руководства. Руководитель должен принимать также активное участие в улучшении процесса.
Если руководство не демонстрирует своими действиями, что качество так же важно, как, скажем, стоимость или время поставки продукта, остальные члены коллектива в компании не будут считать вопрос качества одним из главных критериев в оценке их работы со стороны руководства и их внимание к нему будет ослаблено. Таким образом, стратегия качества должна базироваться на непосредственном участии высшего руководства в обеспечении качества, тогда она будет успешной. Вот почему вовлеченность руководства в процесс обеспечения качества, поставлена во главе важнейших элементов, составляющих базу стратегии TQM.
Руководители организации должны создать в организации такой микроклимат, при котором сотрудники будут максимально вовлечены в процесс достижения поставленных целей .
Принцип главенствующей роли руководства реализуется путем следующих действий:
- активность поведения.
- понимание и реагирование на изменения внешней среды.
- принятие во внимание потребностей всех участников сделок – владельцев, потребителей, персонала организации, поставщиков, общества.
- создание ясного видения перспектив организации.
- определение целей и реализация стратегии для достижения целей.
- установление разделяемых всеми ценностей и этических принципов на всех уровнях организации.
- создание атмосферы доверия и искоренение страха в организации.
- обеспечение персонала необходимыми ресурсами и полномочиями в действиях с осознанием ответственности.
- вдохновение и поощрение персонала, оценка вклада каждого сотрудника в общее дело.
- создание условий для открытых и честных коммуникаций.
- обучение персонала, наставничество .
Весь персонал – от высшего руководства до рядового сотрудника – должен быть вовлечен в деятельность по управлению качеством.
Удовлетворение потребителя качественным продуктом является первостепенной задачей каждого производителя. В то же время, как отмечалось, качество продукта является результатом качества процессов, выход которых он осуществляет (качество процесса равно качеству результатов). Поэтому для обеспечения качественного выхода производитель/поставщик должен обеспечить соответствующее качество самого производственного процесса.
Однако под процессом в TQM понимается не только процесс производства продукта. Существует две точки зрения на то, что представляет собой процесс:
- процесс – это организация ресурсов.
- процесс – это организованная деятельность.
ТQМ исходит из второго определения, рассматривая процесс как любую организованную деятельность, спланированную генерировать предварительно установленный для определенного пользователя выход, обеспечив при этом необходимый вход процесса [12].
У любого процесса есть границы, определяемые начальной стадией (вход) и конечной (выход). Вход часто рассматривают как ресурсы процесса. Выход процесса является результатом преобразования или набора преобразований. Процесс выполняет свою деятельность, используя ресурсы. С этой точки зрения можно дать определение процессу: это совокупность взаимосвязанных ресурсов и деятельности, которая преобразует входящие элементы в выходящие.
Процессы в любой компании по своей сущности могут быть трех видов:
- индивидуальный процесс, выполняемый отдельными индивидами.
- функциональный, или вертикальный процесс, отражающий деятельность компании по вертикали и соответствующий ее структуре взаимодействия руководителей, отделов, подразделений и служащих компании.
- деловой или горизонтальный процесс, который пересекает по горизонтали деятельность компании и представляет собой совокупность взаимосвязанных интегрированных процессов .
Фокусировка внимания на процесс означает, что главным фактором является профилактика, а не исправление допущенных ошибок. Влияние на процесс, а не на результаты процесса – базовая концепция управления процессами компании, работающей в условиях TQM. Нельзя ожидать конечного результата, а затем исправлять ошибки, необходимо влиять на сам процесс, чтобы не допустить их.
Основой управления процессами являются следующие показатели эффективности:
- затраты на реализацию процесса.
- длительность процесса.
- показатели качества процесса.
Чтобы реализовать принцип процессного подхода необходимо предпринять следующие действия в организации:
- определение процесса достижения желаемого результата.
- установление и измерение «входа» и «выхода» процесса.
- согласование процесса с функциями организации.
- оценка возможных рисков.
- четкое распределение полномочий, ответственности и подотчетности в управлении процессом.
- определение внутренних и внешних потребителей и поставщиков, прочих участников процесса.
- концентрация внимания в процессе принятия решения на этапах процесса, потоках, средствах измерения, потребностях в обучении, оборудовании, методологии, информации, материалах и других ресурсах, необходимых для достижения желаемого результата .
На основе этого принципа организация должна определить процессы проектирования, производства и поставки продукции или услуги, в итоге управление результатами процесса переходит в управление самим процессом. Следующим этапом на пути к ТQМ является оптимизация использования ресурсов в каждом выделенном процессе, базирующаяся на строжайшем контроле над использованием всех видов ресурсов и поиске возможностей для снижения затрат на производство продукции (оказание услуг).
Во всех организациях, будь они производственными предприятиями, банками, магазинами, университетами или отелями, и вне их всегда имеет место ряд «цепочек качества» взаимосвязанных процессов, включающих в себя поставщиков и потребителей. Концепция внутренних и внешних потребителей и поставщиков составляет основу всеобщего качества.
Эффективность деятельности организации можно повысить за счет создания и управления системой взаимосвязанных процессов. Это означает, что организация должна стремиться к объединению процессов создания продукции или услуг с процессами, позволяющими отследить соответствие продукции или услуги потребностям заказчика.
Принцип системности управления реализуется за счет следующих действий:
- определение системы путем установления процессов, влияющих на заданные цели.
- структуризация системы для достижения цели оптимальным способом.
- понимание взаимозависимости между процессами в системе.
- непрерывное совершенствование системы на базе оценки и аттестации.
- установление в деятельности приоритета согласованности ресурсов.
Только при системном подходе к управлению станет возможным эффективное использование обратной связи с потребителем для формирования стратегических планов и интегрированных в них планов по качеству .
Организация должна не только отслеживать возникающие проблемы, но и после тщательного анализа со стороны руководства предпринимать необходимые корректирующие и предупреждающие действия для предотвращения повторного появления таких проблем в будущем.
Цели и задачи основываются на результатах оценки степени удовлетворенности заказчика (полученной в ходе обратной связи) и на показателях деятельности самой организации. Улучшение должно сопровождаться участием руководства в этом процессе, а также обеспечением всеми ресурсами, необходимыми для реализации поставленных целей.
Принцип постоянного совершенствования реализуется следующим образом [19]:
- определение в качестве цели каждого сотрудника организации непрерывного совершенствования продукции, процессов и систем.
- использование периодической оценки вместо установленных критериев качества для определения области возможного совершенствования.
- постоянное повышение производительности и эффективности всех процессов.
- поощрение профилактических действий.
- обеспечение всех сотрудников организации соответствующим обучением, методиками и инструментами непрерывного совершенствования, такими, как, например, цикл Деминга, методы реинжиниринга, инноватики и т.д.
- создание системы мер для установления, отслеживания и стимулирования улучшений.
Эффективные решения основываются только на достоверных данных. Источниками таких данных могут быть, например, результаты внутренних проверок системы качества, рекламации и претензии потребителей и т.д. Кроме того, информация может основываться на анализе предложений сотрудников организации по поводу снижения издержек, повышения производительности и т.д.
Принцип фактической обоснованности решений прослеживается в таких проявлениях и действиях организации, как:
- проведение измерений, сбор целевых данных и информации.
- обеспечение достаточно полными, достоверными и точными данными и информацией.
- анализ данных и информации.
- понимание значимости подходящих статистических методов.
- принятие решений и выполнение действий, базирующихся на результатах логического анализа соотношения практического опыта и интуиции.
Каждая организация тесно связана со своими поставщиками, поэтому целесообразно налаживать с ними взаимовыгодные отношения в целях дальнейшего расширения возможностей деятельности организации.
Принцип поддержания взаимовыгодных отношений с поставщиками реализуется в таких проявлениях и действиях организации, как [15]:
- определение и выбор ключевых поставщиков.
- установление отношений партнерства с поставщиками на основе баланса между краткосрочными целями и долгосрочными планами, как организации, так и общества в целом.
- создание простых и открытых взаимосвязей.
- инициирование совместного совершенствования продукции и процессов.
- совместное однозначное определение потребностей потребителей.
- обмен информацией и планами на будущее.
- признание достижений поставщиков.
Практика показывает, что квалифицированное использование методологии ТQМ обеспечивает организации следующие преимущества:
- Увеличение прибыли.
- Обеспечение экономической устойчивости фирмы и рационального использования всех видов ресурсов.
- Улучшение имиджа и репутации фирмы.
- Повышение качества управленческих решений.
- Внедрение новейших достижений.
- Увеличение производительности труда.
- Повышение качества и конкурентоспособности продукции.
- Рост степени удовлетворенности клиентов .
Таким образом, современная концепция управления качеством – это концепция управления любым целенаправленным видом деятельности, позволяющая достигнуть успеха не только в сфере производства, но и в государственном и муниципальном управлении, сфере услуг и других областях [12].
1.2. Японские модели управления качеством при организации производства
В Японии после окончания Второй мировой войны совершенствование качества при организации производства возвели в ранг государственной политики.
В Японии была создана система управления качеством, в которой всеобщий контроль качества представляет собой единый процесс обеспечения качества повсеместно на предприятиях, этот процесс осуществляется всем персоналом от президента до простых работников. Основные подходы к управлению качеством в японских моделях сводятся к следующим моментам [22]:
- Узнать запросы потребителей.
- Узнать, что будут покупать потребители.
- Определить затраты, необходимые для достижения качества.
- Предупредить возможные дефекты и претензии.
- Предусмотреть корректирующие воздействие.
- Исключить необходимость проверки.
В 1967г. на 7-м Симпозиуме по управлению качеством были названы шесть особенностей японской модели управления качеством [11]:
- Участие всех звеньев в управлении качеством.
- Подготовка кадров и обучение методам качества.
- Деятельность кружков качества.
- Инспектирование деятельности по управлению организацией производства.
- Использование статистических методов.
- Общенациональные программы по управлению качеством.
В Японии были разработаны и применены свои инструменты управления качеством. Сегодня всем хорошо известны эти «семь инструментов»:
- Вовлечение в процесс обеспечения качества каждого сотрудника фирмы.
- Использование статистических методов контроля над качеством.
- Создание системы мотивации.
- Поощрение обучения, повышения квалификации.
- Организация кружков качества, поддерживающих низшую иерархическую ступень управления.
- Создание команд (временных коллективов) из специалистов, заинтересованных в решении конкретной проблемы.
- Превращение проблемы обеспечения качества в общенациональную задачу .
В японских системах управления качеством впервые была использована четырехуровневая иерархия качества, в которой угадывается основной принцип концепции ТQМ – ориентации на удовлетворение текущих и потенциальных запросов потребителей (рисунок 2).
Рисунок 2 - Японская иерархия качества
Наиболее известны в настоящее время следующие системы управления качеством, распространенные в Японии:
- Кружки качества (Quality Сircle).
- Программа «Пяти нулей».
- Система JIT (Just-In-Time).
- Система КАНБАН.
Профессор Каору Исикава, один из коллег знаменитого Деминга, предложил идею создания знаменитых Кружков качества (QС). Первоначальной целью таких кружков было обучение персонала японских компаний статистическим методам контроля. Такое обучение стало проводиться в японских компаниях в 60-х годах для вовлечения сотрудников в работу по совершенствованию качества.
Сегодняшние Кружки качества в Японии – это добровольные объединения работников организаций различного уровня и разных областей деятельности, собирающиеся в свободное от работы время с целью поиска мероприятий по совершенствованию качества. Обычно такие кружки имеют свои девизы («Думай о качестве ежеминутно», «Качество решает судьбу фирмы» и т.п.) и действуют на основе следующих принципов:
- добровольности участия.
- регулярности собраний.
- конкретности решаемых проблем.
- выявления, изучения и оценки проблем качества в ходе обсуждения .
Кружки качества очень популярны в Японии: первый кружок был зарегистрирован в 1962г., к началу 1965г. в Японии было 3700 кружков, а в настоящее время их насчитывается более 300 тысяч.
Кружки качества являются методом обучения и поощрения персонала, интересы которого, в свою очередь, учитываются в процессе деятельности организации. Используя простые статистические инструменты, люди работают в группах, обсуждая, анализируя и решая различные проблемы, нацеленные чаще всего на стоимость, безопасность и продуктивность. Также их работой является подготовка предложений по усовершенствованию продукции или услуг компании. Основные результаты деятельности кружков качества представлены на рисунке 3.
Японская система управления качеством на производстве ориентирована на предотвращение возможности допущения дефектов. На японских предприятиях большую популярность завоевала программа «пяти нулей», суть которой сводится к тому, что каждый рабочий не должен делать следующее [11]:
- принимать дефектную продукцию с предыдущей операции;
- создавать условия для появления дефектов;
- передавать дефектную продукцию на следующую операцию;
- вносить изменения в технологию;
- повторять ошибки.
Рисунок 3 - Воздействие кружков качества
Программу «пяти нулей» невозможно было реализовать без максимального использования человеческих ресурсов. И это первым доказал на практике вице-президент фирмы «Toyota» по производству Таичи Охно, создавший концепцию Just-In-Time (JIT) -«делать все вовремя», которая обеспечивает «пять нулей» (ноль запасов, ноль отказов, ноль дефектов) в организации производства и позволяет сократить время от момента получения заказа до момента поставки готового продукта потребителю. Именно совместная оптимизация качества, издержек производства, пунктуальность и тщательность выполнения работ позволяют, в конечном счете, увеличить долю рынка, производительность и прибыльность производства [13].
Система JIT ведет к эффективным действиям по доставке только требуемых товаров или услуг в «правильном» количестве, в «правильное» время и место. При этом под «правильными» понимаются характеристики, которые ожидают как внутренние, так и внешние потребители. Каждая фаза производства в системе JIT заканчивается изготовлением нужной («правильной») детали именно в тот момент, когда она требуется для последующей операции. Если изготавливаемая деталь будет нужна через час, то она и должна быть изготовлена не раньше, чем через час. Все неиспользуемые какое-то время запасы являются непроизводительными расходами и составляют издержки производителя. Складирование впрок – это выброшенные деньги, время и нерациональное использование площади: таков принцип «Toyota».
В этом суть концепции JIT, означающей все делать только в том количестве, с тем качеством и в то время, которое требуется непосредственно Вашим потребителям (внутренним и внешним) .
Практически все перечисленные выше принципы управления качеством были воплощены в микрологистической системе корпоративного управления производством и снабжением КАНБАН (KANBAN), внедренной в корпорации Тоуоtа Моtоrs и позволившей сократить производственные запасы на 50%, а товарные – на 8%.
Система КАНБАН начинает изготавливать конкретный образец продукции только тогда, когда на нее есть определенный заказчик (потребитель).
Начиная с 1970-х годов, опыт Японии в области управления качеством при организации производства постоянно изучается во всем мире. Однако необходимо принимать во внимание то, что специфика японской системы управления качеством особенно обусловлена национальными традициями и социально-экономическими особенностями развития японской промышленности.
Глава 2. Особенности управления в компании Toyota
2.1. История фирмы Toyota
В мировом рейтинге автомобильных производителей «Toyota» сегодня занимает третью позицию и догоняет лидеров – General Motors и Ford.
Киичиро Тойода стал отцом компании, но история Toyota также неразрывно связана и с отцом самого Киичиро, с Сакичи Тойодой. Сакичи считается одним из самых знаменитых японских изобретателей. Он владел фабрикой по производству ткацкого оборудования, которое он сам изобретал и проектировал. Так что Toyota была изначально построена на базе компании, являвшейся мировым лидером, правда, всего лишь в производстве ткацкого оборудования. Главным было то, что Тойодой-старшим был разработан особый принцип действия ткацкого станка, который и снискал продукции компании такую популярность: как только рвалась нить, станок автоматически прекращал свою работу для того, чтобы не портить ткань. Этот принцип, как утверждают представители компании, стал залогом успеха и автомобилей Toyota. Известно, что на заводах компании существует правило: как только хоть у одного из рабочих на конвейере возникнет проблема, он должен остановить всю линию, чтобы не допустить брака.
Качество первых автомобилей, выпущенных Тойодой в 1936 году, можно было назвать каким угодно, скорее всего, американским, но никак не японским. Деньги, вырученные от продажи патента на производство ткацкого оборудования, были потрачены на выпуск модели Toyota AA. За месяц выпустили 150 машин.
В 1935 году была завершена работа над первым пассажирским автомобилем, получившим название Model A1 (впоследствии AA) и первым грузовиком Model G1, а в 1936 году автомобиль Model AA был запущен в производство. Тогда же была произведена первая экспортная поставка – четыре грузовика G1 отправились в северный Китай. После Второй мировой войны, в 1947 году, началось производство еще одной модели – Toyota Model SA, а в 1950 году, в условиях жесточайшего финансового кризиса, компания пережила первую и единственную забастовку своих рабочих.
В 50-х годах проводились разработки собственных конструкций, обширные исследования, расширялся модельный ряд – появился внедорожник Land Cruiser, такая известная ныне модель, как Crown.
В 1961 году выпущена модель Toyota Publica – небольшой экономичный автомобиль, быстро ставший популярным. В 1962 году Toyota отметила выпуск миллионного за свою историю автомобиля. Шестидесятые годы стали периодом улучшения экономической ситуации в Японии, и, как следствие, бурного роста продаж автомобилей.
1970-е годы ознаменовались строительством новых заводов и постоянными техническими усовершенствованиями агрегатов. Начинается производство таких моделей, как Celica (1970), Sprinter, Carina, Tercel (1978), Mark II. Tercel стал первым переднеприводным японским автомобилем. В 1972 году с конвейера сходит 10-миллионный автомобиль Toyota.
В 1982 году начинается выпуск модели Camry. К этому моменту Toyota окончательно утвердилась в роли крупнейшего автомобильного производителя Японии, занимающего третье место в мире по объемам производства. В 1983 году Toyota подписывает многолетнее соглашение с General Motors, а в следующем году начинается производство автомобилей на их совместном предприятии в США. В 1986 году перешагнут еще один рубеж – выпущен уже 50-миллионный автомобиль марки Toyota. Появляются на свет новые модели – Corsa, Corolla II, 4Runner.
Одним из главных событий 80-х годов можно считать появление такой марки, как Lexus – подразделения Toyota, созданного для выхода на рынок автомобилей высокого класса. С появлением же Lexus в секторе роскошных дорогих машин положение изменилось. Уже через год после основания Lexus, в 1989 году были представлены и поступили в продажу такие модели, как Lexus LS400 и Lexus ES250.
Toyota продолжает свою мировую экспансию – открываются филиалы во все новых и новых странах мира и развиваются те, что уже были открыты. Тогда же вышла Хартия Земли (The Earth Charter) – как реакция на усиливающиеся экологические веяния в обществе. Экология оказала на развитие Toyota большое влияние; были разработаны планы и программы по защите окружающей среды, а в 1997 году была создана модель Prius, оснащенная гибридным двигателем (Toyota Hybrid System). Помимо Prius, гибридными двигателями были оснащены модели Coaster и RAV4.
Кроме этого, в 90-е годы Toyota успела выпустить свой 70-миллионный автомобиль (1991 год), и 90-миллионный (1996).
Toyota – это особый стиль ведения бизнеса. Стоит лишь посмотреть на то, как организована работа в штаб-квартире Toyota в городе на острове Хонсю. Этот город так и называется – Toyota (переименован в 1959 году с открытием второго в городе завода компании). Совсем недавно в городе начал действовать проект Crayton. Он заключается в том, что все сотрудники могут для служебных целей использовать специальные электромобили. Когда сотрудники не нуждаются в них, автомобили просто стоят на специальном терминале, где они заряжаются. Данные о запасе хода каждого из них поступают в компьютер. Когда сотруднику необходимо воспользоваться машиной, он просто подает запрос в компьютер и получает специальный код и указание, какой машиной можно воспользоваться. Такая практика вдвойне удобна – во-первых, воздух города Toyota всегда останется чистым, а во-вторых, каждый сотрудник сможет беспрепятственно воспользоваться надежным транспортом. Конечно, двигаются эти автомобили не так уж быстро, зато оборудованы на славу.
Этот проект – всего лишь тестовый. Главное в политике Toyota – то, что она всегда направлена в будущее. Инженерам мало того, что единственным гибридным автомобилем, пользующимся устойчивым спросом, остается Toyota Prius, они, очевидно, считают, что сделали для охраны окружающей среды недостаточно, и продолжают искать способ производства недорогого электромобиля, который не будет отличаться по характеристикам от своего собрата, питающегося бензином.
В отношении к работе заключается еще одна уникальная черта компании. Достаточно показательным является то, что на заводах была всего одна забастовка. В каких бы тяжелых условиях ни оказалась компания, работники все равно будут поддерживать ее и сделают все возможное для того, чтобы помочь выбраться из кризиса. Когда все заводы Toyota пострадали от наводнения, рабочие практически безропотно восприняли новость о том, что им придется работать в две последующие субботы, из которых одна была национальным праздником.
С таким потрясающим подходом администрации компании и рядовых рабочих можно ожидать, что успех станет еще более ощутимым. Многие американцы сегодня заявляют о том, что лучше настоящего японского качества ничего нет. Единственное, что, может быть, пока удерживает Toyota на третьем месте среди автопроизводителей, так это то, что американцы – крайне патриотичная нация. Если это возможно – они выберут американское, свое, родное.
На сегодняшний день Toyota – один из крупнейших мировых производителей автомобилей. Безусловно, она также является крупнейшим японским автопроизводителем, выпускающим более 5,5 миллионов машин в год, что примерно равно одной машине каждые шесть секунд. В группе Toyota – множество компаний, как автомобильных, так и занимающихся многими различными областями. В 2002 году Toyota вступила в новую сферу, приняв участие в автогонках Formula 1.
Сейчас Toyota свыше 45% продукции производит на своих 46 заводах, расположенных вне Японии, практически во всех частях света, включая Африку. Причем доля зарубежного производства в компании за последние 10 лет удвоилась, демонстрируя быстрый рост. На всех заводах за рубежом используется в основном местный персонал с привлечением на первых этапах на ключевые позиции в управлении японских менеджеров. На всех без исключения заводах действует развитая система постоянного обучения TPS (Toyota Production System, производственная система Toyota, первоисточник возникшей позднее в США концепции Lean Production, бережливого производства), которую не минует ни один работник. Так что и Кения, и Венесуэла, и Пакистан, те же США – тоже не Япония, но Toyota удается поддерживать свою культуру повсеместно.
2.2. Организация управления производством
Организация управления производством фирмы Toyota была разработана и усовершенствована «Тойота Мотор Корпорейшн» и после 1973г. была принята многими другими японскими компаниями. Основной целью системы является снижение издержек. Она помогает также увеличить норму оборота капитала (отношение общего объема продаж к общей стоимости основных производственных фондов) и повышает эффективность работы фирмы в целом. Даже в периоды медленного роста система управления производством Toyota позволила обеспечить прибыль посредством уменьшения цен необычным образом: с помощью ликвидации излишних материальных запасов или рабочей силы.
Система управления производством Toyota привлекательна тем, что, ставя целью снижение издержек производства, она устраняет из производства ненужные элементы. Основной принцип гласит: производство необходимых деталей в нужное время и в нужном количестве.
Реализация этой концепции позволяет ликвидировать ставшие ненужными промежуточные узлы и готовые изделия.
Хотя снижение издержек производства является наиболее важной задачей на
Toyota, оно может быть достигнуто при решении трех промежуточных подзадач:
1) оперативное регулирование объема и номенклатуры производства, что помогает системе приспосабливаться к ежедневным и ежемесячным изменениям в количестве и номенклатуре спроса;
2) обеспечение качества, что позволяет организовать снабжение каждой последующей операции деталями высшего качества со стороны смежников;
3) активизация работников, которая должна осуществляться, коль скоро система использует трудовые ресурсы на пути к главной цели.
Эти три подзадачи не могут быть осуществлены изолированно. Основная задача, заключающаяся в снижении издержек производства, недостижима без решения подзадач, и наоборот.
Глава 3. Toyota – мировой лидер в области управления качеством на рынке автомобилестроения
3.1. Модели управления качеством, применяемые Toyota при организации производства
Управление качеством на фирме Toyota основано на четырнадцати основных принципах:
Раздел I: Философия долгосрочной перспективы.
Принцип 1. Принимай управленческие решения с учетом долгосрочной перспективы, даже если это наносит ущерб краткосрочным финансовым целям.
Используй системный и стратегический подходы при постановке целей, причем все оперативные решения должны быть подчинены такому подходу. Осознай свое место в истории компании и старайся вывести ее на более высокий уровень. Работай над организацией, совершенствуй и перестраивай ее, двигаясь к главной цели, которая важнее, чем получение прибыли. Концептуальное понимание своего предназначения – фундамент всех остальных принципов.
Раздел II. Правильный процесс дает правильные результаты.
Принцип 2. Процесс в виде непрерывного потока способствует выявлению проблем.
Перестрой технологический процесс так, чтобы создать непрерывный поток, эффективно обеспечивающий добавление ценности. Сократи до минимума время, которое незавершенная работа находится без движения.
Создавай поток движения изделий или информации и налаживай связи между процессами и людьми, чтобы любая проблема выявлялась немедленно.
Этот поток должен стать частью организационной культуры, понятной для всех. Это ключ к непрерывному совершенствованию и развитию людей.
Принцип 3. Используй систему вытягивания, чтобы избежать перепроизводства.
Сделай так, чтобы внутренний потребитель, который принимает твою работу, получил то, что ему требуется, в нужное время и в нужном количестве. Основной принцип: при системе «точно вовремя» запас изделий должен пополняться только по мере их потребления.
Принцип 4. Распределяй объем работ равномерно (хейдзунка): работай как черепаха, а не как заяц.
Устранение потерь – лишь одно из трех условий успеха бережливого производства. Устранение перегрузки людей и оборудования и сглаживание неравномерности графика производства не менее важны. Этого часто не понимают в компаниях, которые пытаются применять принципы бережливого производства.
Принцип 5. Сделай остановку производства с целью решения проблем частью производственной культуры, если того требует качество.
Качество для потребителя определяет твое ценностное предложение.
Используй все доступные современные методы обеспечения качества.
Позаботься о том, чтобы в организации существовала система поддержки, готовая к оперативному решению проблем и принятию корректирующих действий.
Принцип 6. Стандартные задачи – основа непрерывного совершенствования и делегирования полномочий сотрудникам.
Используй стабильные, воспроизводимые методы работы, это позволит сделать результат более предсказуемым, повысит слаженность работы, а выход продукции будет более равномерным. Это основа потока и вытягивания.
Принцип 7. Используй визуальный контроль, чтобы ни одна проблема не осталась незамеченной.
Используй простые визуальные средства, чтобы помочь сотрудникам быстро определить, где они соблюдают стандарт, а где отклонились от него.
Создавай простые системы визуального контроля на рабочих местах, способствующие поддержанию потока и вытягивания.
По возможности сократи объем отчетов до одного листа, даже если речь идет о важнейших финансовых решениях.
Принцип 8. Используй только надежную, испытанную технологию.
Технологии призваны помогать людям, а не заменять их. Часто стоит сначала выполнять процесс вручную, прежде чем вводить дополнительное оборудование.
Новые технологии часто ненадежны и с трудом поддаются стандартизации, а это ставит под угрозу поток. Вместо непроверенной технологии лучше использовать известный, отработанный процесс.
Прежде чем вводить новую технологию и оборудование, следует провести испытания в реальных условиях.
Отклони или измени технологию, которая идет вразрез с твоей культурой, может нарушить стабильность, надежность или предсказуемость.
Раздел III. Добавляй ценность организации, развивая своих сотрудников и партнеров.
Принцип 9. Воспитывай лидеров, которые досконально знают свое дело, исповедуют философию компании и могут научить этому других.
Лучше воспитывать своих лидеров, чем покупать их за пределами компании.
Лидер должен не только выполнять поставленные перед ним задачи и иметь навыки общения с людьми. Он должен исповедовать философию компании и подавать личный пример отношения к делу.
Принцип 10. Воспитывай незаурядных людей и формируй команды, исповедующие философию компании.
Создавай сильную, стабильную производственную культуру с долговечными ценностными ориентациями и убеждениями, которые разделяют и принимают все.
Неустанно обучай людей работать в команде на общую цель. Освоить работу в команде должен каждый.
Принцип 11. Уважай своих партнеров и поставщиков, ставь перед ними трудные задачи и помогай им совершенствоваться.
Уважай своих партнеров и поставщиков, относись к ним, как к равноправным участникам общего дела.
Создавай для партнеров условия, стимулирующие их рост и развитие. Тогда они поймут, что их ценят. Ставь перед ними сложные задачи и помогай решать их.
Раздел IV. Постоянное решение фундаментальных проблем стимулирует непрерывное обучение.
Принцип 12. Чтобы разобраться в ситуации, надо увидеть все своими глазами (генти генбуцу).
Решая проблемы и совершенствуя процессы, ты должен увидеть происходящее своими глазами и лично проверить данные, а не теоретизировать, слушая других людей или глядя на монитор компьютера.
В основе твоих размышлений и рассуждений должны лежать данные, которые проверил ты сам.
Принцип 13. Принимай решение, не торопясь, на основе консенсуса, взвесив все возможные варианты; внедряя его, не медли (немаваси).
Немаваси – это процесс совместного обсуждения проблем и потенциальных решений, в котором участвуют все. Его задача – собрать все идеи и выработать единое мнение, куда двигаться дальше. Хотя такой процесс и занимает довольно много времени, он помогает осуществить более масштабный поиск решений и подготовить условия для оперативной реализации принятого решения.
Принцип 14. Станьте обучающейся структурой за счет неустанного самоанализа (хансей) и непрерывного совершенствования (кайдзен).
Как только процесс стабилизировался, используй инструменты непрерывного совершенствования, чтобы выявить первопричины неэффективной работы, и принимай действенные меры.
Создай такой процесс, который почти не требует запасов. Это позволит выявить потери времени и ресурсов. Когда потери очевидны для всех, их можно устранить в ходе непрерывного совершенствования (кайдзен).
Оберегай базу знаний об организации своей компании, не допускай текучести кадров, следи за постепенным продвижением сотрудников по службе и сохранением накопленного опыта.
При завершении основных этапов и окончании всей работы произведи анализ (хансей) ее недостатков и открыто говори о них. Разработай меры, которые предупредят повторение ошибок.
Вместо того чтобы изобретать колесо, когда начинаешь новую работу или когда появляется новый менеджер, научись стандартизовать лучшие приемы и методы .
Таким образом, Дао Toyota представляет собой фундамент производственной культуры Toyota, а такая культура обеспечивает эффективное функционирование производства.
Рисунок 4 - Потери на сборочной линии шасси грузовых автомобилей
Рассмотрим пример ручной сборки шасси грузовика на сборочной линии (рисунок 4). Оператор производит много действий, но лишь немногие из них добавляют изделию ценность, которая важна для потребителя. В данном случае выявлено лишь три операции, которые добавляют ценность. Ряд других операций также необходимы, хотя они не создают ценности .
Например, оператор должен протянуть руку, чтобы взять инструмент. Задача состоит в том, чтобы на операции, которые не добавляют изделию ценность, затрачивалось как можно меньше времени. Для этого инструменты и детали должны подаваться как можно ближе к месту сборки.
Toyota выявила семь основных видов потерь – действий или затрат, не добавляющих ценности при осуществлении производственных и бизнес-процессов, которые перечислены ниже. Эти потери возможны не только на производственной линии, но и при разработке продукта, принятии заказов и в делопроизводстве. Существует и восьмой вид потерь, который можно добавить к списку.
1. Перепроизводство. Производство изделий, на которые не поступало заказа, ведет к избытку запасов и порождает такие потери, как излишек рабочей силы и складских помещений, а также затраты на транспортировку.
2. Ожидание (потери времени). Рабочие, которые наблюдают за работой автоматического оборудования, простаивают в ожидании очередной рабочей операции, инструмента, деталей и т.д. или просто сидят без работы из-за отсутствия деталей, задержек в ходе обработки, простоя оборудования и нехватки мощностей.
3. Лишняя транспортировка или перемещение. Перемещение незавершенного производства на большие расстояния, порождающее неэффективность при транспортировке, а также перемещение материалов, деталей и готовых изделий на склад и со склада.
4. Излишняя обработка. Ненужные операции при обработке деталей. Неэффективная обработка из-за низкого качества инструмента или непродуманного конструктивного решения, которая влечет за собой лишние движения и ведет к появлению дефектов. Потери, вызванные завышенными требованиями к качеству.
5. Избыток запасов. Избыток сырья, незавершенного производства или готовых изделий увеличивает время выполнения заказа, вызывает моральное старение продукции, ведет к повреждению готовых изделий, затратам на транспортировку и хранение, задержкам и проволочкам. Кроме того, избыток запасов мешает выявлению таких проблем, как несбалансированность производства, задержки поставок, дефекты, простои оборудования и длительная переналадка.
6. Лишние движения. Все лишние движения, которые приходится делать сотрудникам в процессе работы: поиски того, что нужно, необходимость тянуться за инструментами, деталями и т.п. или заниматься их укладкой. Сюда же относится ходьба.
7. Дефекты. Производство дефектных деталей и исправление дефектов. Ремонт, переделка, отходы, замена продукции и ее проверка ведут к потере времени и сил.
8. Нереализованный творческий потенциал сотрудников. Потери времени, идей, навыков, возможностей усовершенствования и приобретения опыта из-за невнимательного отношения к сотрудникам, которых вам некогда выслушать.
Тайити Оно считал основным видом потерь перепроизводство, поскольку именно оно порождает большую часть остальных потерь. Если компания на любой стадии производственного процесса изготавливает больше изделий, чем нужно потребителю, это неизбежно ведет к избыточным запасам на последующих стадиях производства: детали лежат и ждут очередного этапа обработки. Приверженцы массового или крупносерийного производства могут спросить: «Ну и в чем проблема? Пусть люди и оборудование делают свое дело, производят детали». Проблема в том, что избыток запасов, которые скапливаются, ожидая следующей стадии обработки, влияет на поведение сотрудника, у которого исчезает стимул к постоянному совершенствованию .
Зачем беспокоиться о профилактическом обслуживании оборудования, если его простой не приводит к нарушению процесса сборки? Зачем переживать из-за небольших отклонений качества, если дефектные детали отправляются в общую кучу? А когда дефектная деталь поступит на следующую операцию, где рабочий попытается использовать ее при сборке, обнаружится, что негодные детали производятся уже несколько недель, но об этом никто не знал, ведь они дожидаются своего часа уже давным-давно.
На рисунке 5 эти потери представлены на простой координате времени для процесса литья, механообработки и сборки. При традиционном технологическом цикле большая часть времени, затраченного на обработку материала, представляет собой потери.
Рисунок 5 - Потери при создании добавленной ценности
С точки зрения бережливого производства сначала следует составить карту потока создания ценности в соответствии с траекторией перемещения материала в ходе интересующего процесса. При составлении схемы такого перемещения получают схему, которая называется «диаграммой спагетти». Даже те, кто большую часть жизни проработал на производстве, поражаются полученным результатам. На рисунке 5 видно, что растягиваются очень простые процессы обработки изделия до такой степени, что выявление операций, добавляющих ценность, становится непростым делом .
3.2. Достижения и просчеты фирмы Toyota в организации управления качеством
При традиционном подходе к совершенствованию процесса учитывается локальная эффективность: «посмотри на оборудование, на операции, добавляющие ценность, и сделай период безотказной работы длиннее, рабочий цикл короче, а где можно – замени человека автоматом».
В результате эффективность отдельной операции возрастает, но это не оказывает ощутимого влияния на поток создания ценности в целом. Важно помнить, что большинство процессов включает очень незначительное число операций, добавляющих ценность, и с
|