СКАЧАТЬ РАБОТУ БЕСПЛАТНО -
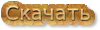
Качество начинается с исследования потребностей. Это самый важный этап жизненного цикла любого товара, так как именно на нем решается общий замысел товара, формируется образ, определяются самые общие характеристики. Ошибки на данном этапе наиболее критичны, так как, если неверно определены потребности, в конце производственной цепочки можно получить товар, который просто не будут покупать. В управлении качеством есть «правило десятикратных затрат». Оно гласит, что затраты на производство некачественной продукции, на обнаружение брака возрастают десятикратно при переходе со стадии маркетинга, проектирования на стадию производства, а также от стадии производства к стадии эксплуатации. Иначе говоря, если исправить какой-то недостаток при проектировании стоит 1000 рублей (скажем, переделать чертеж), но на производстве это обойдется уже в 10 000 рублей (переналадка производственной линии), а после Продажи уже в 100 000 рублей (отзыв партии товара у покупателей).
Качественный товар нельзя сделать на основании плохого проекта, в котором не учтены все особенности изделия, не просчитаны все возможные поломки и отказы, не проанализирована каждая составляющая товара и ее влияние на функционирование изделия в целом, не оптимизирована стоимость изготовления и последующего обслуживания.
Хороший проект необходимо перевести из чертежей и замыслов в физическую форму. Это можно сделать только качественно организовав производство, то есть, спланировав все процессы изготовления и способы контроля. Плохая организация производства, несогласованная и некачественная работа оборудования способны свести на нет все усилия проектировщиков и маркетологов. Вот почему производство и сопровождаемый его поэтапный контроль качества – важнейший этап создания товара.[8]
Великолепно сделанный товар можно упаковать в неудобную или некрасивую упаковку, и через некоторое время потребители начнут высказывать свое недовольство, обратятся к более качественной продукции конкурентов. Можно, конечно, попытаться убедить их, что упаковка – это не главное. Но, как правило, такие доводы не работают. Чтобы продемонстрировать правильность последнего утверждения, достаточно представить себе современный сотовый телефон, который продается в салоне связи не в красочной коробке, а завернутый в салфетку. Вроде бы и телефон тот же, а восприятие – уже совершенно иное. Мало изготовить товар и упаковать его в красочную и безопасную упаковку. Надо еще его сохранить и доставить потребителю. То, как это делается, как организована продажа, насколько она удобна для покупателя – такая же составляющая качества, как и сам товар.
Из всего сказанного выше можно сделать следующий вывод: качество закладывается в товар с самого начала и контролируется на всех стадиях. Качественный товар получается, только если на всех стадиях соблюдаются необходимые требования.
Понятие качества продукции имеет очень важное значение в практической деятельности, потому регламентировано ГОСТом 15467-79 «Управление качеством продукции. Основные понятия. Термины и определения». Согласно этому нормативному документу под качеством понимается совокупность свойств продукции, обусловливающих ее пригодность удовлетворять определенные потребности в соответствии с ее назначением.
Качество продукции имеет первостепенное значение для потребителей, так как именно качество определяет ее потребительскую стоимость. При этом часто повышение качества продукции равнозначно росту ее количества; кроме того повышение качества обычно достигается при меньших затратах, чем увеличение объема выпуска продукции.[3]
2. Нормативная база СМК
Семейство стандартов ИСО серии 9000:2000 состоит из четырех стандартов. Документация системы менеджмента качества дол¬жна включать следующие документы:
− руководство по качеству;
− документированные процедуры, требуемые стандартом ISO 9001:2000;
− документы, необходимые организации для обеспечения уверенности в эффективном планировании, реализации и управлении ее процессами, в том числе рабочие инструк¬ции (описывают отдельные комплексные технологические процессы), контрольные инструкции (описывают отдель¬ные процедуры проведения контрольных и испытательных мероприятий);
− нормативную документацию и техническую литературу. Приведем краткую характеристику каждого из перечисленных видов документации по качеству.[4]
Руководство по качеству охватывает все применяемые элементы стандарта на систему качества, необходимые для предприятия и включает:
− область применения системы менеджмента качества;
− документированные процедуры созданные, для системы менеджмента качества или ссылки на них;
− описание взаимодействия между процессами системы ме-неджмента качества;
− необходимые приложения.
Важнейшим элементом Руководства является регламентация ответственности по системе качества.
Стандарт ISO 9001 и призваны обеспечить качество при проектировании, разработке, производстве, монтаже, обслуживании и состоят из сле¬дующих элементов:
1. Ответственность руководства, в том числе:
1.1. Обязательства руководства
1.2. Ориентация на заказчика
1.3. Политика в области качества
1.4. Планирование
1.5. Ответственность, полномочия и взаимосвязи
1.6. Анализ со стороны руководства
2. Управление ресурсами
2.1. Обеспечение ресурсами
2.2. Человеческие ресурсы
2.3. Инфраструктура
2.4. Производственная среда
3. Выпуск продукции
3.1. Планирование выпуска продукции
3.2. Процессы, связанные с заказчиком
3.3. Проектирование и усовершенствование
3.4. Закупки
3.5. Производство и оказание услуг
4. Изменения, анализ и улучшения
4.1. Общие положения
4.2. Мониторинг и измерения
4.3. Управление несоответствующей продукцией
4.4. Анализ данных
4.5. Улучшения[6]
Рабочие инструкции, в число которых входят:
Технологические карты;
Специальные разделы проектов производства работ;
Схемы операционного контроля.
Управление этим видом документации не регламентируется стандартами ISO-9000.
Контрольные инструкции, в число которых входит:
− входной контроль проектной документации, материалов, деталей, оборудования;
− контроль качества производственных процессов;
− проведение авторского надзора.
Нормативная документация и техническая литература. Данный обширный раздел документации по качеству может быть представ¬лен несколькими подразделами, в том числе отраслевые/общетехнические нормы и стандарты.
Так, в строительстве различают следующие виды нормативных документов: организационно-методические; общие технические нормативные; по градостроительству, зданиям, сооружениям; на инженерное оборудование зданий, сооружений и внешние сети; на строительные конструкции и изделия; мобильные здания и соору¬жения, инвентарь и оснастку; по экономике; справочники, учеб¬ники, методики для описания признанных нормативных положе¬ний.
Концептуальным моментом отечественных норм нового по¬коления является изменение их структуры и статуса:
− нормы предписывают конечные требования к качеству про-дукции, а не методы их осуществления;
− обязательными для исполнения являются нормы, регламен-тирующие безопасность, охрану окружающей среды, а так¬же надежность и долговечность продукции предприятия;
− в технических разделах контрактов должны быть приведе¬ны нормативы, соблюдение которых является обязатель¬ным условием приемки продукции проектов.
Новая Российская система строительных норм находится сей¬час в стадии становления. В новую систему, регламентируемую стро¬ительными нормами и правилами Российской Федерации «Систе¬ма нормативных документов в строительстве.
Основные положе¬ния» (СНиП 10.01-94), входят:
− федеральные нормативные документы (строительные нор¬мы и правила, рекомендательные нормативные документы, а также государственные стандарты Российской Федера¬ции);
− административно-территориальные нормативные докумен¬ты (территориальные строительные нормы);
− производственно-отраслевые нормативные документы (строительно-технологические нормы и нормативные до¬кументы по стандартизации, стандарты предприятий, объе¬динений и научно-технических обществ и технические ус¬ловия).
Отличительной чертой вновь разрабатываемых нормативных документов в области строительства является переход к новым ме-тодическим принципам, которые находят все большее распростра¬нение в практике строительного нормирования и стандартизации технически развитых зарубежных стран. В отличие от традиционно сложившегося так называемого «описательного» или «предписы¬вающего» подхода, когда в нормативных документах приводится подробное описание конструкции, методов расчета, применяемых материалов и т. д., вновь создаваемые строительные нормы и стан¬дарты должны содержать, в первую очередь, эксплуатационные ха¬рактеристики строительных сооружений и изделий, основанные на требованиях потребителя, т. е. цели, которые должны быть достиг¬нуты, но не методы их достижения.
Предполагается, что нормативные документы будут постепен¬но изменяться. Так, в них не будет предписываться, как проектиро¬вать и строить, а будут лишь устанавливаться требования, которые должны быть удовлетворены. Обязательными должны быть только требования по обеспечению безопасности жизни и здоровья граж¬дан, охраны окружающей природной среды, надежности и долго¬вечности возводимых зданий и сооружений, совместимости и вза¬имозаменяемости продукции и применяемых в строительстве тех¬нических решений.
Объемно-планировочные, конструктивные, технологические и другие технические решения, которые ранее регламентировались нормами, будут носить только рекомендательный характер. Эти решения должны приниматься с учетом конкретных условий соот¬ветствующих производств, природно-климатических, социальных и экономических особенностей и национальных традиций респуб¬лик, краев и областей, входящих в Российскую Федерацию.
Система строится на методических и организационных прин¬ципах, отвечающих принятым в работе международных (ISO, EN) и национальных организаций по стандартизации в технически раз¬витых странах. Предусматриваются гармонизация нормативных документов системы с международными стандартами в области строительства и строительным законодательством зарубежных стран, а также сохранение общей нормативной базы строительства стран Содружества Независимых Государств в виде межгосудар¬ственных нормативных документов.
Все работы по обеспечению качества основаны на использовании стан¬дартов Международной организации по стандартизации (ISO), при-знанных в 1988 году в б. СССР в качестве национальных стандартов. В рамках систем управления качеством используют серию стандар¬тов ISO 9000 и эквивалентную ей серию EN 29000
Проектно-сметная документация. Управление проектно-сметной документацией включает в себя процедуры по приемке, согласованию и внесению изменений в проектно-сметную доку¬ментацию. Состав и объемы работ по приемке, согласованию и внесению изменений в проектную документацию определяются требованиями заказчика, государственных стандартов или иных нормативных документов РФ, относящихся к тематике проекта, и закрепляются договором (контрактом) с заказчиком. В качестве основного документа принимается «Инструкция о порядке раз-работки, согласования, утверждения и составе проектной доку¬ментации на строительство предприятий, зданий и сооружений (СНиП 11-01-95)».
Организационно-распорядительная документация. В состав внут-ренней распорядительной документации входит:
− положения о структурных подразделениях, должностные инструкции;
− приказы и распоряжения, подписанные генеральным ди-ректором и уполномоченными им заместителями;
− протоколы производственных совещаний, утвержденные генеральным директором и уполномоченными им замести¬телями;
− резолюции на внутренних служебных документах, подпи-санные генеральным директором и уполномоченными им заместителями;
− все входящие документы.[7]
Важно также понимать, что ИСО 9000 не является стандартом качества продукции или даже качества производственного процесса, но устанавливает стандартные требования к системе качества («система качества – совокупность организационной структуры, методик, процессов и ресурсов, необходимых для общего руководства качеством» – ИСО 8402).
3. Управление качеством продукции или представляемой услуги на любом этапе жизненного цикла товара
ОАО «Азимут» определило для себя основное направление развития – стать «компанией европейского класса». Это может быть достигнуто только за счет высоких требований к качеству, которое для ОАО «Азимут» является основной ключевой целью. Эта цель достигается на основе реализации следующих принципов:
- Ориентации на потребителя. Это наиболее полное выполнение требований потребителя к продукции завода по техническим характеристикам, упаковке, надежному транспортированию, соответствие продукции и производства нормам и законам. Только потребитель может оценить качество продукции. Задача ОАО «Азимут» - немедленно реагировать на его замечания, предложения и предлагать продукцию по приемлемым ценам.
- Рационального использования ресурсов. Сохранение и увеличение ресурсов, снижение затрат, финансовая стабильность достигаются в первую очередь за счет предупреждения несоответствий, постоянного совершенствования продукта, производства и процессов управления.
- Взаимной ответственности. Все работники предприятия являются одновременно заказчиками и поставщиками и ответственны за качество своей работы перед своими внутренними и внешними потребителями.
- Создания социально-психологического климата. Отношения между работниками и руководителями строятся на основе справедливости и признания достижений. При равной квалификации – равные возможности в продвижении по службе.
- Непрерывного обучения. Система постоянного повышения квалификации является основой высокого интеллектуального потенциала ОАО и, соответственно, конкурентного преимущества.
- Сотрудничества с поставщиками. С поставщиками ОАО работает в духе сотрудничества, взаимного доверия и помогает развивать их системы качества.
- Взаимных гарантии работников и акционерного общества. Все работники бережно относятся к имуществу общества, а общество гарантирует им безопасные условия труда и сохранение экологической среды.
- Руководство предприятия берет на себя обязательства по обеспечению ресурсами основных направлений развития акционерного общества, реализации политики и доведения её до каждого работника.
Кроме общезаводских целей в области качества на ОАО «Азимут» разрабатываются цели для каждого структурного подразделения предприятия. Отдел системы качества разработал следующие цели в области качества на 2006-2008 годы:
1) Сертификация системы качества по модели ИСО 9002, что позволит предприятию:
- минимизировать риск отказа покупателя от продукции или ее возврата (вследствие нестабильности качества) и связанных с этим потерь и ухудшения экономических показателей деятельности предприятия;
- повысить конкурентоспособность ОАО «Азимут» и, как следствие, расширить внутренний рынок и увеличить экспортные возможности;
- повысить престиж предприятия в глазах потребителей и общества, укрепить доверие к фирменной марке. Следствием сертификации, таким образом, станет рост заказов, поступающих как от отечественных, так и от зарубежных потребителей и увеличение объемов сбыта продукции;
- повысить эффективность менеджмента качества за счет использование недвусмысленных процедур и рационального распределения полномочий и ответственности в области качества;
- улучшить отношение исполнителей к работе вследствие наличия необходимых инструкций, обучения, более простого представления информации о проблемах качества, ощущения надежности работы;
- получить возможность «говорить на одном языке» со специалистами по качеству на международном уровне.
2) Сертификация системы управления окружающей средой по ИСО 14000.
3) Совершенствование системы качества предприятия с целью продвижения ее к TQM.
4) Постоянное повышение квалификации персонала в области качества.
Система качества – это целостная система, состоящая из организационно самостоятельных, но взаимосвязанных элементов. На ОАО «Азимут» по каждому элементу разработаны методологические инструкции.
В качестве путей совершенствования системного управления качеством на ОАО «Азимут» можно представить следующие: внедрение статистических методов для анализа данных по качеству и создание подсистемы оценки затрат на качество.
Проанализировать данные по качеству, найти причины брака можно при помощи статистических методов. На ОАО «Азимут» такие методы не внедрены, хотя давно признана целесообразность их внедрения на предприятиях, так как они позволяют:
- изучать и управлять процессами, обнаруживая случайные и закономерные влияния;
- оценивать возможности процессов (технологическая точность);
- самообучаться персоналу;
- управлять персоналом;
- проверять эффективность мероприятий, постоянно улучшать качество продукции.
Статистические методы применяют для сравнения и анализа больших множеств данных, представляя их в какой-либо наглядной форме (диаграмма Парето, столбиковые диаграммы, контрольные карты, причинно-следственные диаграммы)
Одним из методов совершенствования управления качеством является построение контрольных карт.
Рассмотрим правила построения карт. Исходные данные:
- объем подгрупп больше, чем 50;
- среднее число дефектов или дефектных изделий равно или больше 4;
- если фактический объем подгруппы отличается на ±50% от среднего объема подгруппы, то нужно либо выбросить эту точку, либо вычислить для нее индивидуальные контрольные пределы.
В качестве примера применения контрольных карт для качественных переменных построим р-карту для определения динамики появления дефектов при производстве анилина, одного из продуктов ОАО «Азимут». По данным из таблицы 1. найдем (средний объем подгруппы) и (средний процент брака):
Таблица 1- Исходные данные для построения контрольной карты для доли дефектов в объеме произведенного анилина за январь 2009 года
Номер партии Объем партии (п, переменный), т Число дефектов в выборке (пр) Процент брака в каждой выборке, %
1 50 2 4,0
2 50 10 20,0
3 60 6 10,0
4 65 4 6,2
5 50 5 10,0
6 50 10 20,0
7 55 5 9,1
8 60 8 13,3
9 50 2 4,0
10 55 4 7,3
Внешний контрольный предел (ВКПр) и нижний контрольный предел (НКПр) определим по формуле
или в цифровом выражении:
Еще одним распространенным и эффективным статистическим методом, позволяющим произвести анализ причин появления того или иного дефекта является метод построения причинно-следственной диаграммы Исикавы. Данный метод позволяет:
- разбить проблемы на составляющие;
- показать, как взаимодействуют различные причины, при помощи построения иерархии этих причин;
- представить многие причины графически.
Построение диаграмм включает следующие этапы:
-выбор результативного показателя, характеризующего качество изделия (процесса и т. д.);
- выбор главных причин, влияющих на показатель качества. Их необходимо поместить в прямоугольники («большие кости»);
- выбор вторичных причин («средние кости»), влияющих на главные;
- выбор (описание) причин третичного порядка («мелкие кости»), которые влияют на вторичные;
- ранжирование факторов по их значимости и выделение наиболее важных.
На рисунке 1. построена причинно-следственная диаграмма Исикавы для дефекта «высокая доля примесей в анилине». Рассматривая рисунок можно сделать вывод, что отклонения в качестве получаемого анилина из-за сырья возникают вследствие наличия примесей в нитробензоле (воды и сернистых соединений), перебоев с поставкой нитробензола, недостаточного запаса водорода в газгольдере, а также из-за плохого качества катализатора. Персонал тоже выступает причиной низкого качества анилина, в частности из-за невнимательности, прогулов и текучести кадров. В процессе производства данного вида продукции были выявлены причины отклонений от установленных требований из-за технологии производства. Ошибки, вызывающие брак, возникают на стадии очистки нитробензола от примесей (от воды и от сернистых соединений), при отгонке летучих соединений и на стадии получения товарного анилина. Также на качество продукта влияет то, что внедренная новая линия производства еще недостаточно отлажена.
Причинно-следственная диаграмма Исикавы позволяет увидеть многие проблемы, но не дает ответа на вопрос какие из них решать в первую очередь, чтобы добиться улучшения качества продукции или процесса. В данном случае применяется метод построения диаграммы Парето.
Рис. 1. Причинно-следственная диаграмма Исикавы для дефекта «высокая доля примесей в анилине»
Диаграммы Парето – это специфические формы столбчатых графиков. С их помощью можно установить приоритеты для выявления основных проблем. Эти диаграммы могут помочь руководству получить ясную картину и определить, где можно оказать самое большое воздействие.
Принципы построения диаграммы Парето следующие:
- все выявленные при построении причинно-следственной диаграммы Исикавы проблемы делятся на категории. При производстве анилина такими категориями являются: А – сырье; Б – технология; В – персонал; Г – оборудование; Д – окружающая среда;
- определяют, какая категория содержит наибольшее число проблем, распределяют категории на диаграмме в порядке убывания слева на право;
- строят кумулятивную линию, которая наглядно показывает вес каждой категории в общей массе проблем.
На рисунке 2. построена диаграмма Парето относительно причин дефекта – высокая доля примесей в готовом продукте (анилин) по данным причинно-следственной диаграммы Исикавы.
Рис. 2. Диаграмма Парето для анализа причин дефекта «высокая доля примесей в готовом анилине»
Рисунок 2 позволяет сделать вывод, что в первую очередь следует направить усилия на устранение причин дефекта категории А – сырье, так как они составляют 30 % в общей массе причин. Здесь возможны следующие варианты действий:
- либо работа с поставщиками (поиск новых, у которых качество нитробензола, катализаторов лучше или переговоры со старыми поставщиками о путях повышения качества их продукции);
- либо приобретение оборудования, которое позволит очистить сырье от примесей.
Таким образом, можно сделать вывод, что внедрение таких статистических методов, как контрольные карты для качественных признаков (р-карты), причинно-следственная диаграмма Исикавы и диаграмма Парето, позволят производить глубокий анализ причин отклонений от установленных требований в процессе производства и рационально использовать ресурсы при устранении этих причин.
Кроме использования статистических методов управления качеством немаловажно внедрить и экономический механизм управления качеством, который будет включать в себя оценку затрат на качество. Это необходимо сделать потому что, любые действия по устранению причин дефектов, освоению нового продукта или предотвращению дефектов влекут за собой дополнительные затраты. Данные затраты являются, несомненно, затратами на качество. На ОАО «Азимут» во избежание неоправданных расходов целесообразно осуществлять управление этим видом затрат.
Для внедрения на ОАО «Азимут» можно предложить следующую классификацию затрат на качество:
- для новых продуктов производить подсчет единовременных затрат. Сюда входят затраты, связанные с проведением научно-исследовательских, опытно-конструкторских и технологических работ, организационно-технических мероприятий, техническим перевооружением и реконструкцией производств, подготовкой, повышением квалификации и переподготовкой кадров и других мероприятий, направленных на повышение качества продукции и ее конкурентоспособности;
- для текущего анализа производить расчет затрат: связанных с содержанием подразделений по управлению качеством продукции или реализацией функций управления качеством продукции; с предотвращением дефектов в продукции, их выявлением и устранением, а также потери, обусловленные передачей далее по технологической цепочке и потребителям дефектной продукции.
Следующим шагом при формировании подсистемы оценки затрат на качество является определение расчетных формул
В соответствии с выбранной классификацией затрат определим формулы для каждого вида затрат:
- затраты, связанные с содержанием подразделений по управлению качеством продукции (Зукп) рассчитываются по формуле:
где Фiукп – месячный фонд оплаты труда i-го подразделения по управлению качеством продукции, руб.;
Аiукп – сумма амортизационных отчислений на возмещение стоимости основных производственных фондов, находящегося в распоряжении i-го подразделения;
п – число подразделений предприятия по управлению качеством.
Затраты на проведение какого-либо мероприятия по предупреждению, выявлению и устранению дефектов определяются по следующей формуле:
где аi – величина амортизационных отчислений на возмещение стоимости i-го вида оборудования, руб./год;
n – виды оборудования;
m – виды сырья;
cj – количество j-го вида сырья, израсходованного на переделе в месяц;
цj – оптовая цена j-го вида сырья;
Фа – заработная плата, начисленная за реализацию данного мероприятия.
Потери, связанные с наличием дефектов в полупродуктах и готовой продукции , определяются по следующей формуле:
где Сn – фактическая себестоимость единицы готовой продукции;
Д – доход (прибыль) от реализации единицы готовой продукции;
Nc – объем списанной продукции в натуральном выражении;
Cu – стоимость устранения дефекта в единице продукции;
Nu – объем продукции, в которой произведено устранение дефекта.
Произведем расчет затрат на качество при производстве 100 тонн анилина за февраль 2010 года (таблица 2).
Таблица 2 - Затраты на обеспечение качества анилина на ОАО «Азимут» за февраль 2010 года
Наименование Затраты, тыс. руб. Доля затрат на качество в цеховой себестоимости, %
Затраты, связанные с содержанием подразделений по управлению качеством продукции 4,17 1,01
Затраты на проведение какого-либо мероприятия по предупреждению, выявлению и устранению дефектов, в том числе: 23,56 5,68
- амортизационные отчисления на возмещение стоимости оборудования 7,56 1,82
- стоимость сырья, материалов, энергоносителей 11,00 2,65
- оплата труда работников, участвующих в реализации данного мероприятия 5,00 1,20
Потери, связанные с наличием дефектов в полупродуктах и готовой продукции, в том числе: 71,72 17,29
- потери, связанные со списанием продукции с неустранимыми дефектами 12,31 2,96
- потери, связанные с устранением дефектов 59,43 14,33
Итого затрат на качество 99,43 23,99
Цеховая себестоимость анилина 414,51 100%
Из таблицы видно, что затраты на качество при производстве 100 тонн анилина составляют 23,99 % от общей суммы цеховой себестоимости, причем наибольший удельный вес имеют потери, связанные с наличием дефектов в полупродуктах и готовой продукции (17,29 %).
Вывод в такой ситуации можно сделать следующий: уровень затрат на качество необходимо понизить, что позволит уменьшить себестоимость продукции. Например, уменьшение потерь, связанных с наличием дефектов в полупродуктах и готовой продукции на 10% повлечет за собой уменьшение себестоимости на 1,7 % или 7,2 тыс. руб. Также необходимо направлять больше средств на проведение какого-либо мероприятия по предупреждению, выявлению и устранению дефектов и одновременно понижать потери, связанные с дефектами, тем самым повысится эффективность системного управления качеством.
Заключение
Качество – это объективно существующая совокупность свойств и характеристик изделия, которая определяет его пригодность для использования по назначению. Эти свойства и характеристики формируются при создании продукции и в зависимости от требований заказчиков могут быть самыми разнообразными как по уровню, так и по сочетанию. Поэтому под обеспечением качества логично понимать процесс формирования необходимых свойств и характеристик продукции. И не только процесс, но и результат, когда говорят, что требуемое качество обеспечено.
Для обеспечения качества требуется:
- необходимая материальная база (покупные изделия, материалы, технологическое и испытательное оборудование, средства измерений, здания, сооружения, транспорт и т.д.);
- квалифицированный персонал, заинтересованный в хорошей работе;
- глубоко продуманная организационная структура и четкое управление предприятием в целом и управление качеством – в частности.
Список использованной литературы
1. Версан В.Г., Чайка И.И. Системы управления качеством продукции. М.: Изд. Стандартов. 2007. - 150с.
2. Гиссин В.И. Управление качеством продукции. Р.-на-Дону: Феникс. 2008. - 255с.
3. Гличев А.В. Основы управления качеством продукции. М.: Изд. Стандартов.2007. - 80с.
4. Леонов И.Г., Аристов О.В. Управление качеством и количеством продукции. М.: Изд. Стандартов. 2006. - 200с.
5. Мюллер К. Некоторые аспекты внедрения системы качества в промышленности. Стандарты и качество. 2007. - №3 - С. 58-64.
6. Свиткин М.З. От семейства стандартов ИСО 9000 к всеобщему менеджменту качества. Стандарты и качество. 2008. - №9 - С. 43-47.
7. Швец В.Е. Менеджмент качества в системе современного менеджмента. Стандарты и качество. 2006. - №6. - С 48-50.
8. Шишкин И.Ф. Метрология, стандартизация и управление качеством. М.: Изд. Стандартов. 2007. - 325с.
|